Custom Hand Tools and Custom Socket Set Cost Saving
Custom Metal Part Cost Reduction?
As a customer, how could you help the factory make lower price quotation?
With no threat, no fighting, is it possible?
Metal production cost is evaluated by total processing time and the machine depreciation cost. When we develop the new product, Tien-I R&D will always think if there is possible way to
improve the processing cost by drive down the complexity of processing procedure and shorten the overall processing time without sacrifice the quality and the function.
Here are some of Tien-I engineers’ suggestions
1.) Avoid unnecessary Deep Hole
Two factors add cost up, the tap size and hole depth. The deeper hole is, the longer processing time takes which mean more expensive. Sometimes the product components made separately and then assembling afterward is good choice. Split the complex parts. There is no best way but through several experiments to find the better way.
We can also use wire EDM or other deep processing way, but it could be the same cost or worse.
In addition, the tap size is also critical. The bigger the more expensive. But too small doesn’t mean cheap. Because the machine can’t work with such the small size and it leaves no choice but hand drill. Standard size is always welcome. Therefore, it is better to discuss with the factory to see the “comfortable” tape size range, while you design the product.
2.) Not each Tolerance should move to Third Decimal.
For the critical dimension, it is totally correct to insist the must-do tolerance. But not each dimension need to be perfectly precisely (like +/- 0.005), especially when the product no
need to be assembled.
Too tight tolerance will lead to dramatic increase in the machining time, because the machine speed get lower. Besides, the overall cost rise due to higher defective rate. Of course, we can process with more precise equipment but it also means the equipment cost getting higher.
3.) Standard Size is King
Turning tools or taper tool for machine are available for standard size, such as inch 1/4", 1/8". The processing mechanics will appreciate you very much if you avoid non-standard size design. Special dimension or specification are totally equal to $$$. There is some exception, such as your demand is stable and huge, like Apple iPhone so you can creat your own standard.
4.) If possible, increase the order quantity
The more you order, the more quantities for the machining factory to proceed. Which the mold and experiment time cost can be shared, and also higher bargain power against raw material.
Compared with the world standard, Tien-I processing capacity is much flexible, from 100 to 1,000,000 pieces. But it doesn't mean the necessary fixed cost disappear. Perhaps it absorbed by the partnership and long-term relationship between the manufacturer and the customers.
Above suggestion from Tien-I's engineer team and experienced mechanics. Appreciate their contribution.
Tien-I is
specialized at custom special hand-tool or metal parts, Our clients include German and USA Top Tool Brands, as well as Japan Machine company.
Need quotation, contact Tien-I experienced team
If you like to know more about how Tien-i making the right quotaiton for pro hand tool brand, simply click below button:
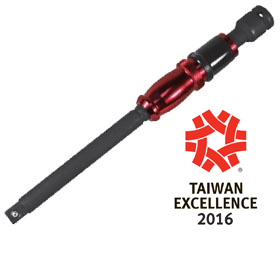
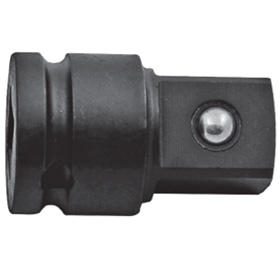
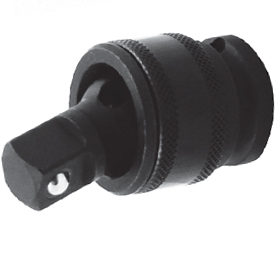
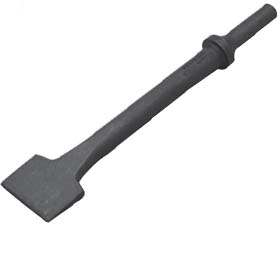
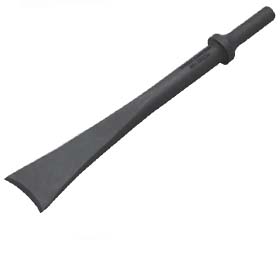
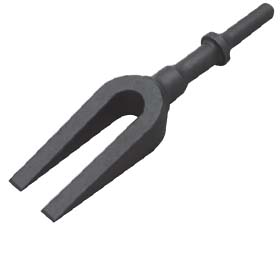
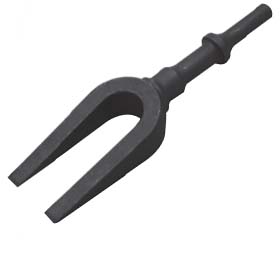
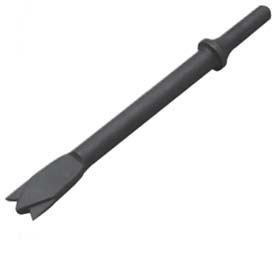
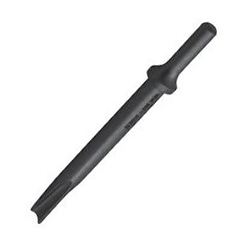
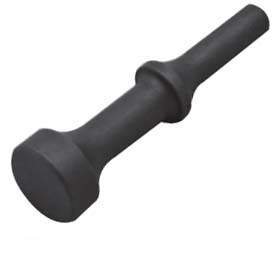
.jpg)
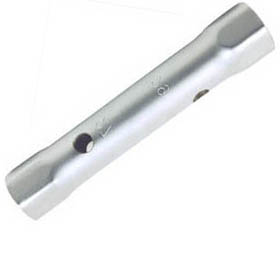
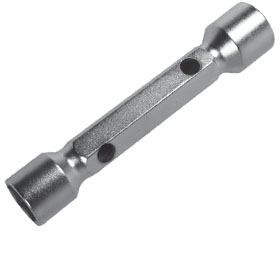
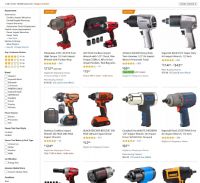
.jpg)
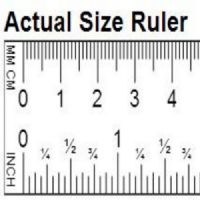
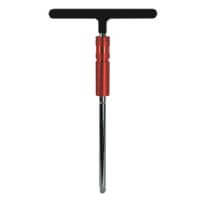